
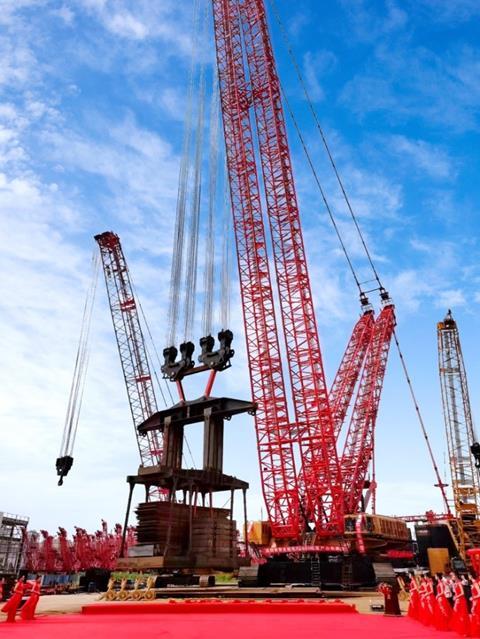
The crane was positioned at a radius of 86m and was even extended to over 142m for certain lifting operations.ĭespite the site being located in the windiest region of Brazil, the fact that the SK350 has a 14 m/s operating speed reduced the impact of the challenging wind conditions and enabled Mammoet to complete the lifting operation ahead of schedule.
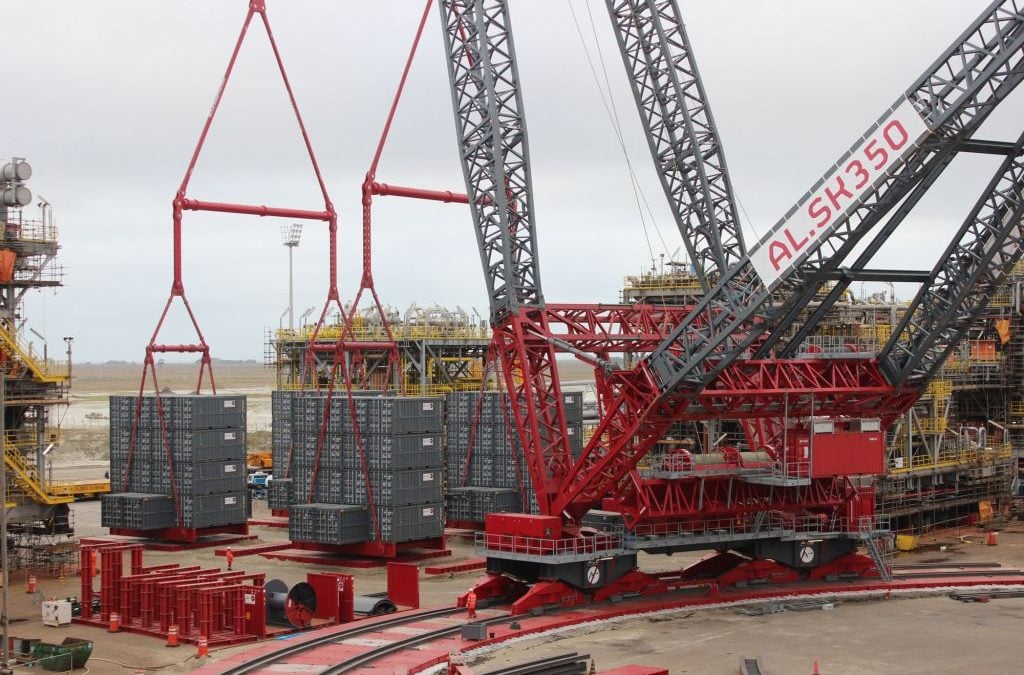
One of the advantages of using the SK350 was its ability to lift all of the modules from their fabrication location in the yard and minimize the need for additional equipment on site to transport the modules.Īs the SK350 cranes give a much greater reach, it was able to lift all modules from their fabrication location, unlike alternative solutions which required the modules to be moved closer to the crane using SPMTs.įor the 3,000t lift of module ‘M09’ – the combined M09A and M09B – the SK350’s 4,000t winch system and high-speed slew was used.
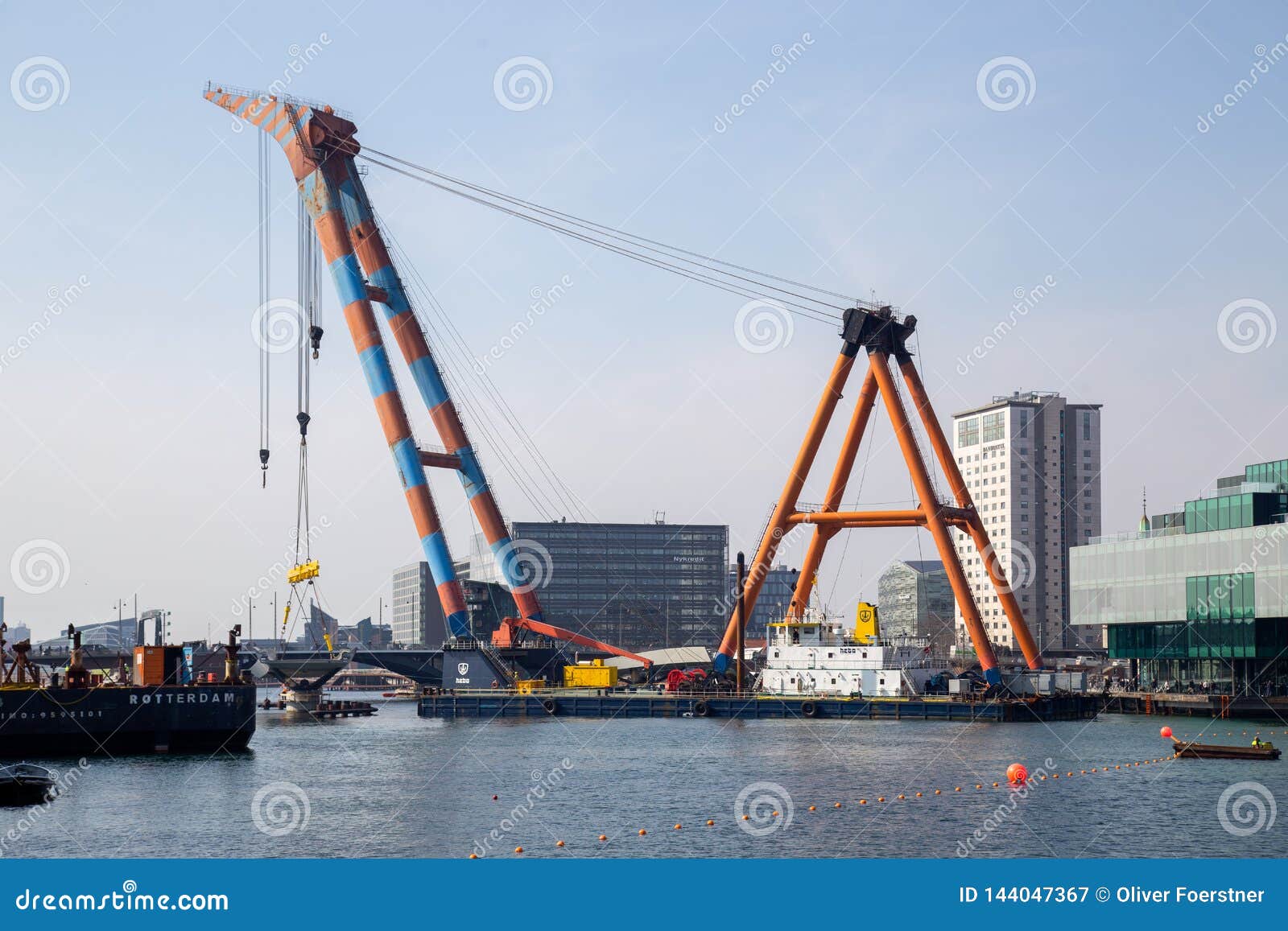
The crane is equipped with a 4,000t main winch and 600t auxiliary quick winch systems. The main boom is a 130m long A-frame design on a very stable 18m wide base. Mammoet’s SK350 crane was rigged in its current biggest configuration with 49m ballast radius and 4,000t ballast. The SK350’s high capacity offered the customer the opportunity to fabricate and join modules M09A and M09B on site, avoiding the longer process of installing them separately.

The modules ranged in weight and dimension, between 80t to 3,000t. The lift of 3,000t was the largest commercial lift by a land-based crane. Well done one and all.Mammoet performed the heavy lifting and installation of 40 modules, weighing up to 3,000t, onto the P-74 FPSO (Floating Production, Storage and Offloading) vessel in the south of Brazil. We have continued to learn from Unit 1 to safely deliver a quality product.
#Huge crane lift install
Simon Parsons, NI Area, Site & Civils Director says: “This significant lift is testament to everyone involved – from the teams who fabricated it, to those on Unit 2 who’ve delivered the civil-works schedule enabling us to install it and also the lifting team themselves. The optimum construction time between the two reactors at Hinkley Point C is around 12 months and this installation highlights this gap is being maintained. This allowed work to focus on areas most critical to the project’s schedule. The achievement is all the more impressive as the project deliberately switched materials and labour away from unit two during the pandemic when numbers on site were limited and suppliers were impacted. The prefabricated ring, which is 47 metres in diameter and 17 metres high, forms a reinforced cylinder around the nuclear reactor. This “replication effect” will benefit the identical Sizewell C project in Suffolk. The ring was built 25% more quickly than the same part on unit one, requiring thousands of hours less labour to manufacture. The installation shows how building an identical copy of the first reactor drives efficiency and saves time. It has this week placed the first huge steel ring section onto the second reactor building, just 11 months after the same operation on the first reactor. Big Carl, the world’s biggest crane has been in action again at Hinkley Point C near Burnham-On-Sea.
